Nel finissaggio tessile esistono due principali strategie di sviluppo dei macchinari in modo che consumino meno energia: tecnologie che saltino determinati passaggi produttivi per accorciare il flusso, oppure l’utilizzo di componenti tecnologici di ultima generazione come motori, controlli elettrici ed elettronici che riducano il consumo di energia.
Un altro modo di risparmiare energia è quello di ottimizzare i processi di finissaggio: l’ideale oggi sarebbe riuscire a ridurre l’utilizzo di vapore, acqua o elettricità nei diversi step e adottare soluzioni tecniche che siano in grado di limitare o recuperare in parte l’energia consumata.
COMPAS, macchinario compattatore e di finissaggio

Un esempio pratico è un sistema indiretto di raffreddamento dell’acqua che riduca la temperatura del nastro di gomma del compattatore.
Con questo sistema è possibile recuperare l’acqua attraverso un raffreddatore che mantiene la temperatura al giusto livello, risparmiando circa 3 m3 di acqua all’ora secondo i calcoli eseguiti con il macchinario compattatore e di finissaggio COMPAS di Sperotto Rimar per la maglia e i tessuti piani.
Quest’acqua, completamente pulita, può essere recuperata e riutilizzata di continuo nel macchinario.
L’utilizzo delle sostanze chimiche nel finissaggio è un tema delicato. Nei processi di finissaggio a secco in genere si tratta di ammorbidenti o resine che migliorano l’aspetto e la mano del tessuto, caratteristiche poi trasferite al capo finale.
Compas conferisce una mano setosa che solo in parte deriva dagli ammorbidenti usati, ma principalmente da materiali speciali nel design del macchinario. Grazie a questa tecnologia, tutelare l’ambiente non significa che gli utilizzatori finali devono scendere a compromessi sulla piacevolezza della mano del tessuto.
NOVA, impianto per il lavaggio in solvente dei tessuti sintetici
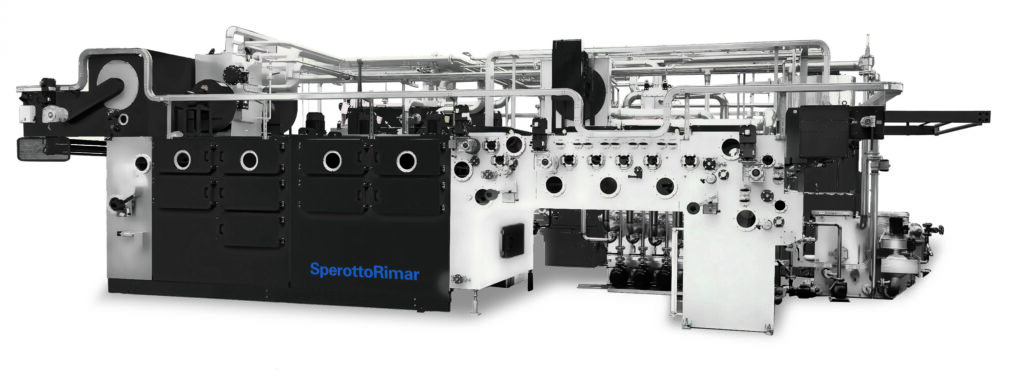
Inoltre, sofisticati impianti come NOVA per il lavaggio in solvente dei tessuti sintetici della Sperotto Rimar sono in grado di riciclare più del 99% delle sostanze chimiche utilizzate nel processo e rimuovono quasi del tutto l’olio contenuto del tessuto.
Ciò impedisce il rilascio di fumi inquinati nei successivi processi termici; in aggiunta, l’energia necessaria per asciugare il solvente è 10 volte inferiore di quella per asciugare lo stesso quantitativo di acqua. In più, oggi i macchinari per il lavaggio in solvente sono più sostenibili rispetto al passato, in quanto lavorano con un sistema di ricircolo chiuso in cui l’aria e il solvente sono trattati e riciclati correttamente.